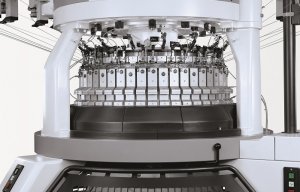
Mayer & Cie. targets shoe upper market
Knitting Industry spoke to Wolfgang Müller, Sales Director Mayer & Cie. about the company’s and circular knitting’s part in this booming market segment.
2nd August 2017
Knitting Industry
|
Albstadt
Interview with Wolfgang Müller, Sales Director Mayer & Cie.
Knitted fabrics are growing increasingly popular as an upper material for both sports and fashion shoes and leading circular knitting machine manufacturer Mayer & Cie. offers several machines that are suitable for their manufacture, including the new OVJA 1.6 EE – 3WT/2WT – the first machine in the company’s product range that was specially designed for this purpose. Knitting Industry spoke to Wolfgang Müller, Sales Director Mayer & Cie. about the company’s and circular knitting’s part in this booming market segment.
Knitting Industry (KI): With flat knitted shoe uppers, knitting times are comparatively long but there is almost zero waste during production. Circular knitting is obviously much more productive than flat knitting but the waste levels must be quite high. Can you comment on this?
Wolfgang Müller (WM): Let’s first look at the economic aspect and at the production process as a whole. As a rule, standard filament yarns, mostly polyester, are used in circular knitting of shoe uppers. This means the yarn is less significant as a cost factor. And the output is much higher – ten to twenty times higher. So, in economic terms the wastage is not that relevant.
Looking at the ecological aspect, we have to put the wastage, which in fact exists with circular knitted shoe uppers, in perspective. First of all, not all flat knitting machines produce knit-to-shape, i.e. with no waste. We assume only 50 percent work this way. Another half either works with partly engineered shoe panels or rectangular shoe panels. Especially with the latter, we’re looking at the same waste levels we have with circular knitted shoe uppers.
Furthermore, due to higher productivity, energy consumption per piece produced on a circular knitting machine is about five times lower than on a flat knitting machine working with knit-to-shape. And, not to forget, standard polyester may be recycled.
KI: We believe that as many as 40,000 flat knitting machines have been sold worldwide for shoe upper production since the launch of the Nike Flyknit in 2012. How big is the circular knitting machine sales potential for shoe uppers?
WM: It is very hard to say how big the market may become in the future. In producing shoe uppers, circular knitting is definitely much more productive than flat knitting. So, assuming we could replace 50 per cent of flat knitting machines, we could possibly reach 1500 machines. Then we’d expect a further benefit because circular knitting is likely to replace some weaving and warp knitting too. So in the end, we’d probably be looking at a market of 3,000 to 5,000 circular knitting machines for shoe upper production over the next five years or so.
KI: Knitted fabric shoe uppers are very popular now for both fashion shoes and sports shoes. Can you give any indication on the total market size for knitted shoe uppers and which shoe types are best produced on circular knitting machines?
WM: Different types of leisure shoes can be produced with circular knitted upper material. That includes various sorts of sports shoes, such as running and fitness shoes. Even high-performance shoes in the outdoor and hiking segment come with upper materials produced on a circular knitting machine.
But at present it is impossible for us to give an indication of the total market size for knitted shoe uppers.
KI: Warp knitting completely dominates the shoe upper market. What are the main advantages of circular knitting over warp knitting in shoe upper production?
WM: The main advantage of circular knitting technology over warp knitting in shoe upper production is its variety of patterns and how easy they are to produce. On a warp-knitting machine several warp beams always need to be prepared, which involves work. That is only worthwhile if the material is manufactured in large quantities.
A circular knitting machine knits multi-coloured spacer fabrics and structures simply by pressing a button, as it were, using design software. That is why smaller batches in the desired colour combination can be produced profitably on a circular knitting machine.
KI: Mayer & Cie. machines offer a range of options for shoe uppers in jacquard, stitch transfer and spacer structures. Is there a machine that offers all-round versatility for shoe uppers?
WM: The perfect all-round machine that can both produce hole structures and provide the wide range of structures that double needle selection offers does not yet exist. In principle we have a concept of this kind that we could adapt for shoe uppers. But as always in life, you have to lower your sights here or there. The greater the pattern flexibility, the more we lose in terms of productivity.
That is why we attach great importance to being able to offer an optimal solution for every use that the customer requests. We definitely have optimal solutions at the ready in our OVJA range and the Technit D3. They offer jacquard patterns and spacer or hole structures, for example, combined with multi-coloured jacquard and striped patterns. And then there is a machine for coarse gauge and another for spacer fabrics with a high level of abrasion resistance.
A machine that combines more or less all of these features is feasible, as noted above. We have a concept for one, but it would do so at the expense of productivity. We are nonetheless looking into offering this all-rounder machine as well in the medium term.
Further information
Business intelligence for the fibre, textiles and apparel industries: technologies, innovations, markets, investments, trade policy, sourcing, strategy...
Find out more