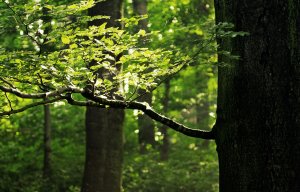
Lenzing aligns climate targets with Paris Agreement goals
Kingwhale is a vertically integrated company, controlling the entire production process from fibre spinning through textile manufacturing to garment construction.
14th December 2020
Knitting Industry
|
Taipei, Taiwan
Kingwhale, a responsible manufacturer of performance textiles, has joined the RE100 global initiative, pledging to 100% renewable electricity by 2040, and becoming the first textile mill in Asia-Pacific to do so.
Renowned for its range of technical knits and fleeces, Kingwhale is a vertically integrated company, controlling the entire production process from fibre spinning through fabric manufacturing to garment construction. Additionally, the company says, it has long placed an emphasis on sustainability, with its proprietary technologies resulting in manufacturing practices that minimize energy consumption, reduce waste, and utilize fewer resources.
RE100, led by the international non-profit The Climate Group, states its mission as, ‘To accelerate change towards zero carbon grids at scale’. The Climate Group brings together influential organizations, such as Kingwhale, that are committed to taking ambitious actions to combat climate change, Kingwhale explains.
We understand quite well that textile production can be very demanding on our natural resources, and that’s why we take sustainability very seriously
The announcement of Kingwhale’s was announced via the RE100 Twitter account on 9 December 2020. “Our latest Taiwanese member is the textile manufacturer Kingwhale Corporation! Joining #RE100 today, they have committed to sourcing 100% renewable electricity by 2040. We hope more companies will follow their lead and join #RE100. @ClimateGroup @CDP,” the tweet proclaimed.
As a bluesign system partner and OEKO-TEX Standard 100 certified company, Kingwhale says it is already regarded as an industry leader with regards to its environmental stewardship. In fact, its L.I.T. (Low Impact Technology) is lauded for its waste reduction and efficiency, the company says. The innovative yarn technology modifies the molecular structure of polyester, and accordingly, the dyeing process for these modified fibres requires 60% less water for dye preservation, 15% less dyestuffs to achieve colour, and 22% less electricity for heating and cooling, adds Kingwhale.
“The RE100 initiative was the next logical step for us,” said James Huang, President of Kingwhale. “We understand quite well that textile production can be very demanding on our natural resources, and that’s why we take sustainability very seriously. For years Kingwhale has set an example for our industry, showing others it’s possible to create great products while minimizing waste and energy consumption, and now I hope others will join us in our commitment to 100% renewable electricity.”
Since its founding in 1992, Kingwhale’s reputation has grown not only for the unrivalled quality of its products, but also because of its efficiency, according to the company. “We’ve leveraged our full expertise in textiles to build a vertically integrated company that controls the entire manufacturing process—from fibre spinning to fabric weaving to final garment production. Today, Kingwhale textiles are commonly found among the most iconic fashion, sportswear, and lifestyle brands,” Kingwhale concludes.
Business intelligence for the fibre, textiles and apparel industries: technologies, innovations, markets, investments, trade policy, sourcing, strategy...
Find out more