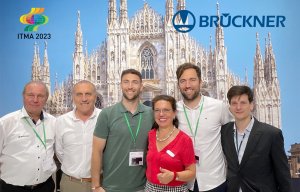
Campos chooses Brückner Power-Frame stenter
The focus of this innovative concept was above all an absolutely low-tension material flow and the shortest possible fabric path.
9th August 2016
Knitting Industry
|
Leonberg
Brückner Textile Technologies, a leading Germany based textile machinery manufacturer, has partnered with Compagnie Mauricienne de Textile Ltée (CMT) for a machine specialised in the finishing of highly sensitive knitted fabric, with an elastane content of up to 15%.
The focus of this innovative concept was above all an absolutely low-tension material flow and the shortest possible fabric path in order to reduce residual shrinkage, the company reports.
CMT is a leading garment manufacturer, headquartered in Mauritius, with design and marketing offices in the UK and France. The company is specialised in fast-fashion jersey-wear for high-street retailers in Europe and the US.
From the pin-on-point to the interior of the dryer, the machine characterises a belt that supports the moist fabric over the complete width. According to the manufacturer, this is particularly important for sensitive knitted fabric and prevents sagging and fabric distortions. The belt is coated with a Teflon, which has undergone special treatment, and this technology has proved its effectiveness in avoiding marks and snags on delicate fabric, the company reports.
As part of the design of this special machine, Brückner used the patented split-flow air circulation system. This system is said to achieve a considerable output increase through aerodynamic optimization, with even reduced energy consumption and an air circulation that treats the fabric gently.
The additional counter-arrangement in each half-zone, in combination with the patented Venturi-mixing, aims to allow the customer to adapt the circulating air temperatures for each process individually in each half-zone. Additionally, the air impingement above and below the fabric web is adapted to the drying profile of the fabric via two speed-controlled fans. This leads to an ideal temperature distribution and to an extremely homogeneous and gentle air impingement on the fabric web.
CMT, a leader in the jersey-wear industry, has the largest vertically-integrated manufacturing plant in the Sub-Saharan region. The company was set up in 1986 by Mr François Woo Shing Hai and Mr Louis Lai Fat Fur. All the CMT Directors have been with the company from its conception in 1986, leading and guiding the growth and development of the company ever since.
Back in 1998, CMT and Brückner jointly installed the first Brückner stenter with the patented split-flow air circulation technology. This line is today still perfectly in operation and has been established as one of the work-horses of CMT's production line, the company reports.
True to its forward-thinking core vision, CMT corroborated its commitment to the environment by backing the acquisition of the machine with a Brückner heat-recovery system. The heat from the exhaust air is used to pre-heat fresh air. This fresh air is admitted to the drying process at several points so that the drying process can take place constantly with the best possible fresh air/exhaust air ratio, according to the company.
In addition, the consumption of thermal energy can be visibly reduced and thus allow a significant reduction in the production cost. CMT uses the new finishing line mainly for superior finishing processes with delicate fabrics.
Positioning itself as a leading producer of system solutions for textile finishing, the family-run Brückner Group has been developing, designing and manufacturing premium lines for the dry finishing of textiles and technical fabric for more than 66 years.
With the technological know-how and decades of experience, Brückner aims to supply customers with tailor-made machine concepts that would cater for new applications for finer knitted fabric and more delicate fibres.
Business intelligence for the fibre, textiles and apparel industries: technologies, innovations, markets, investments, trade policy, sourcing, strategy...
Find out more