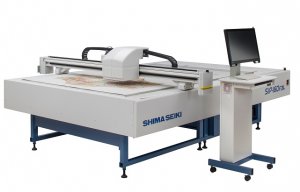
Shima Seiki to present flatbed inkjet printing machine at FESPA 2017
Digital printing surges as fast fashion demands speed.
22nd July 2025
Knitting Industry
|
United Kingdom
Direct-to-garment (DTG) and direct-to-film (DTF) digital textile printing are poised for rapid expansion, according to a new 21-page report by Textiles Intelligence, titled ‘Digital printing direct to fabrics and garments: developments and growth prospects’.
The digital textile printing sector has seen major innovation, driven by advances in automation, ink chemistry and print head technology. These developments have enabled full-colour, customised, and flexible design possibilities on a wide range of fabrics. Importantly, many new machines eliminate the need for pre- and post-treatment processes, making production more resource-efficient, cost-effective and environmentally responsible.
Manufacturers leading in digital textile printing machine development include Brother, ColorJet, EFI Reggiani, Epson, Kornit Digital, Mimaki and Sawgrass.
DTG printing applies inkjet technology directly to garments for vibrant, high-resolution designs, while DTF printing transfers designs via polyester film, producing bold and long-lasting results. Both methods are increasingly aligned with the needs of the e-commerce and fast fashion sectors, which depend on speed, variety and on-demand capabilities.
Their agility makes DTG and DTF ideal for quick design iterations, reduced lead times and small-batch production. These features have made the technologies essential to the modern apparel market, particularly among digital-first brands.
DTF printing has seen particularly explosive growth. An estimated 7 billion items were printed using DTF in 2024, and the method is now used to decorate around half of all T-shirts produced globally. Much of this expansion has been fuelled by investment in China.
Shein, the Singapore-based ultra-fast fashion retailer, has emerged as a pioneer in DTF technology. The company has developed two proprietary in-house methods: Digital Thermal Transfer Printing and Cool Transfer Denim Printing. The latter is noted for its environmental benefits, using 70% less water than traditional denim finishing methods.
The new report is available for purchase via the link below:
Business intelligence for the fibre, textiles and apparel industries: technologies, innovations, markets, investments, trade policy, sourcing, strategy...
Find out more