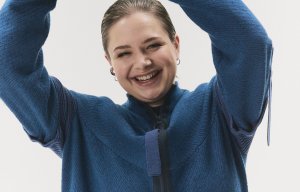
Redefining custom knitwear and textile development
Editor’s View
Swedish School of Textiles knitting lab collaborates with car maker on interior textiles for the Polestar 4 electric SUV coupe.
18th September 2023
Billy Hunter
|
Borås, Sweden
The Swedish School of Textiles’ 1100 square metre Knitting Technology Lab in Borås, Sweden, is one of the most modern and well-resourced University labs in Europe for knitted textiles. Three highly qualified technicians, with extensive industry experience, support academic staff in providing a ‘base education’ to each of the 300 or so new students that join the school each year.
Education in the specialisation of fashion and textile design, textile engineering, masters students, exchange students, teaching programming and more advanced knitting, is all catered for. The knitting laboratory also takes part in research and development projects, both nationally and more and more, internationally. Prototype research for external companies and organizations from around the world is ongoing and the laboratory’s staff also guide PhD students in specific research projects where knitting is an important discipline.
In circular knitting, the laboratory is equipped with a variety of machines, including a range of standard machines as well as more specialised machines like its Mayer & Cie. metal knitting machine, a Relanit 0.8, a Harry Lucas ‘stent knitting’ machine, and Mayer & Cie OVJA E ‘extreme inlay/filling 3D’ machines. The laboratory’s latest circular knitting investment is a Mayer & Cie OVJA 1.6 EE machine.
The laboratory also has a number of flat knitting machines including a Stoll CMS 822HP 5.2 knit and wear, a specially equipped CMS 330TC 6.2, Shima Seiki SWG 091N WHOLEGARMENT machine, Stoll ADF 530KI gauge 7.2 (12-gauge needle hook), and a Shima Seiki N.SVR123 SP shaping machine.
Polestar collaboration
Recently the knitting lab collaborated with advanced EV manufacturer Polestar on the interior of its Polestar 4 electric performance SUV coupe, the second SUV in the brand’s line-up. Polestar is the Swedish electric performance car brand determined to improve society by using design and technology to accelerate the shift to sustainable mobility. Headquartered in Gothenburg, Sweden, its cars are available online in 27 markets globally across North America, Europe and Asia Pacific.
The Polestar 0 project is the company’s ambitious goal of creating a truly climate-neutral production car by 2030. The research initiative also aims to create a sense of urgency to act on the climate crisis, by challenging employees, suppliers and the wider automotive industry, to drive towards zero.
Design cues first seen on Polestar’s concept cars are brought to production in the fastest Polestar production car to date. Polestar 4 is positioned between Polestar 2 and Polestar 3 in terms of size and price.
“With Polestar 4 we have taken a fundamental new approach to SUV coupe design. Rather than simply modifying an existing SUV, giving it a faster roofline and as a result, compromising elements like rear headroom and comfort, we have designed Polestar 4 from the ground up as a new breed of SUV coupe that celebrates rear occupant comfort and experience,” says Thomas Ingenlath, Polestar CEO.
Design
As a design-driven brand, the design of Polestar 4 showcases key elements first shown on the Polestar Precept concept car. This includes eliminating the rear window, which enables a new kind of immersive rear occupant experience. Additionally, the separation of the dual blade front lights with unique Polestar light signature – complemented by the Polestar emblem with precision lighting from below.
Aerodynamic efficiency is maximised by the low nose, retractable door handles, flush glazing with frameless windows, rear aero blades and air flow optimization around the rear light bar.
Built on the premium Sustainable Experience Architecture (SEA) developed by Geely Holding, Polestar 4 is a D-segment SUV coupe with a large body and long, 2,999 mm wheelbase. Overall length is 4,839 mm, width is 2,139 mm and height is 1,544 mm. The resulting generous interior proportions are especially evident in the rear, where occupants experience an intimate environment with reclining seats. Adjustable ambient lighting is inspired by the solar system and adds an extra dimension to the interior, allowing the driver to customize their environment.
The standard full-length glass roof is available with optional electrochromic functionality, allowing for opaque or transparent upward visibility depending on the mood. Thanks to the elimination of the rear window, the glass roof stretches beyond the rear occupants’ heads, creating a truly unique interior ambience. A secondary media and climate control screen is mounted between the front seats to enable rear occupant control.
The interior and its materials have been designed around the theme of ‘soft tech’, drawing inspiration from the fashion and sportswear industries. Colour and material choices for Polestar 4 explore new executions for Polestar – including new exterior colours Storm and Electron, and a unique new interior colour, Mist.
Sustainability
In Polestar 4, more circular and low-carbon materials replace traditional solutions. This includes measures for greater supply chain transparency, like blockchain traceability for risk materials in the batteries. A full lifecycle assessment (LCA), showing the true carbon footprint of the car, will be published alongside the Polestar 4 Product Sustainability Declaration in 2024.
A novel mono-material approach is applied to interior materials, where all layers of certain components are produced from the same base material. This allows them to be recycled more effectively and efficiently by eliminating the need for incompatible materials to be separated before recycling.
New interior materials include a tailored flat knitted textile, which consists of 100% recycled PET, along with bio-attributed MicroTech vinyl and animal welfare-secured Nappa leather upholsteries.
The tailored knit upholstery is a relatively new technique for the automotive industry. First shown in the Precept concept car, the textile is made from 100 % recycled polyester. The material and the design were created by Polestar designers together with the Swedish School of Textiles (Borås Textilhögskolan) and further developed with suppliers.
It is made to fit, producing no offcuts and reduced overall waste on a Stoll ADF 530-32 ki W flat knitting machine in gauge 7.2 (12-gauge needle). More knitted interior textiles, including elements for the dashboard, door panels, speaker mesh and more, were developed on the Knitting Technology Lab’s Mayer & Cie. Relanit 0.8 circular knitting machine, in 12 gauge.
Inlay carpets in the interior are made using recycled PET and floor carpets are made using Aquafil’s Econyl, which includes reclaimed fishing nets. Specific door trim panels are made from NFPP (natural fibre polypropylene), which results in up to 50% less virgin plastic and a weight saving of up to 40%. MicroTech, first introduced in Polestar 3, is a bio-attributed vinyl that replaces crude oil with pine oil in its construction and features a recycled textile backing.
Polestar at the Knitting Technology Lab
In the lab, Polestar’s Maria Uggla, Colour and Material Design Manager, and Komal Singh Colour worked with recycled materials through 3D knitting, a new technology for the automotive industry. This is a sustainable technology where recycled materials can have new uses and the product can be produced in just the right size without waste, Polestar says.
Watch the video of Maria and Komal in the Knitting Technology Lab…
“With our unique infrastructure regarding the development of textile applications, we become an interesting partner for different types of companies, which we are very pleased about. Many collaborative projects with industry lead on to research projects and student projects that develop us as an academic environment as well as companies involved. Through our research and education, we strengthen this ability and look forward to many more exciting collaborative projects in the future,” concludes Mats Tinnsten, Vice-chancellor, University of Borås.
Polestar 4 launches first in China, with production planned to begin in Hangzhou Bay, China, in November 2023. The state-of-the-art Geely-owned production facility operates on 100% renewable electricity.
Business intelligence for the fibre, textiles and apparel industries: technologies, innovations, markets, investments, trade policy, sourcing, strategy...
Find out more