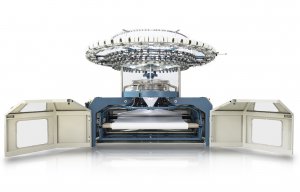
Santoni and Vickers Oils collaborate to power innovation
The leading German provider of industrial machine needles Groz-Beckert presented its innovation at this year’s ITMA trade fair in Barcelona.
9th September 2019
Knitting Industry
|
Albstadt
Groz-Beckert needle SAN SF. © Groz-Beckert
Reduced cleaning requirements and fewer lint-related lines in the knitwear when processing staple fibre yarn in large diameter circular knitting machines is the specialty of the new, patented Groz-Beckert needle SAN SF. The leading German provider of industrial machine needles presented its innovation at this year’s ITMA trade fair in Barcelona.
The new SAN SF special application needle takes account of the fact that, by nature, the processing of staple fibre yarn involves a higher amount of lint that can accumulate in the needle track. It was designed to reduce the associated effects and helps to ensure that the knitting process runs fault-free for longer periods of time without prolonged interruptions for cleaning.
Staple fibre yarns are made by twisting fibres of a respectively defined length. During processing in the knitting machine, yarns like these lose fibres due to friction. Protruding fibre ends can also break off. This results in increased fibre fly, which is deposited in and on the knitting machine. In conjunction with oil, contamination thus occurs, which means that the machine must be cleaned regularly to guarantee problem-free processes.
If the mixture of oil and fibres enters the needle trick, it can accumulate under the needle shank and raise the needle. This leads to differences in the hook position. The result: formation of lines in the knitwear and potential damage to the needle due to contact with other machine elements.
“Here the only remedy is frequent cleaning,” the manufacturer explains. “The machine must be stopped, the needles must be removed and freed from residues in a time-consuming process. The slots of the cylinder must be cleaned. The machine is at a standstill.”
Contamination and dust. © Groz-Beckert
“This is where the new Groz-Beckert SAN SF special application needle comes into play. Its special needle shank geometry prevents dirt from getting under the needles. This means that the machine can run for much longer without the necessity to remove the needles for cleaning even when processing staple fibre yarns and can produce more fabric during the same time.”
The needle back is solid, i.e. without cut-outs. It therefore fills the entire needle trick and leaves no space for residues to accumulate. The needle stays in its position and keeps the needle trick clean for longer – up to three times longer in field tests, according to the company.
“There are humps on the top side of the needle shank. They also help to transport fibres out of the needle trick and to keep them away from the back of the needle. They also support the trick wall if a neighbouring needle butt is overloaded in multi-track machines.”
The SAN SF is said to significantly reduce the frequency of contamination-related lines in the knitted fabric. Knitting mills may benefit from lower costs and higher productivity thanks to reduced cleaning requirements.
Business intelligence for the fibre, textiles and apparel industries: technologies, innovations, markets, investments, trade policy, sourcing, strategy...
Find out more