New General Manager at Karl Mayer Turkey
Warp Knitting/Crochet
Karl Mayer improves training and service in China and Korea
For the Chinese market, Karl Mayer supplies machines which are made in China and provides a whole raft of services. The customer support operations are concentrated in the company’s subsidiary, Karl Mayer Technical Services and its activities include setting up new installations, instant help for individual clients, and advice on how to use the technology. Since the beginning of this year, the company has been systematically training its new service technicians on the
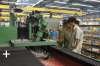
7th October 2010
Knitting Industry
|
Wujin
For the Chinese market, Karl Mayer supplies machines which are made in China and provides a whole raft of services. The customer support operations are concentrated in the company’s subsidiary, Karl Mayer Technical Services and its activities include setting up new installations, instant help for individual clients, and advice on how to use the technology.
Since the beginning of this year, the company has been systematically training its new service technicians on the basis of a specific programme in order to ensure that it can support its customers in China even more efficiently and competently. The professional training given in Germany is the model for the logical management of the qualification and training operations.
The training programme for the future service engineers is slightly shorter than the German version and its contents are extremely focused. The first part covers all the manufacturing operations taking place in Karl Mayer’s Chinese production location in Wujin and lasts six months. During the six months of in-house training, the new trainees work in the production, assembly and needle departments. At the same time, they get to know the Karl Mayer Academy China and the back office operations. By the end of the first part of the training programme, they will have learned a great deal about the machines.
They will then move on to going out on service calls to customers’ plants. The trainee technicians will work alongside experienced colleagues to master all the challenges posed by practical production conditions, and will be able to apply all the knowledge they have accumulated in practice. This second part of the training programme also lasts for six months.
Karl Mayer says that in a sector where there are no organised training facilities, the one year programme, which is intended to prepare the young trainees for their future careers, represents an extraordinary level of commitment on the part of the company and is also an investment that will definitely pay for itself.
With its training programmes, Karl Mayer is in a position to guarantee a high level of service, especially in view of the large number of new installations currently operating in China. For their part, the young school leavers and new graduates will be given a solid basis on which to begin their future careers. “During the training programme, we are able get to know the machines that we will be responsible for servicing in the future – right down to the very last detail,” said Mr. Gan Xian Qing, one of the trainees on the first course. “As service engineers, this will enable us to provide assistance quickly and effectively. When accompanying our experienced service colleagues on service calls, we realised just how important it is to have sound, well-based technical knowledge.”
To improve its service provision in Korea, Karl Mayer has taken on a technician formerly employed by one of its partners, Illies. The new service engineer will therefore be able to concentrate specifically on every aspect of Karl Mayer’s. This arrangement will increase efficiency and provide a wider range of services when going out on service calls to clients’ factories. The new member of the team will have to successfully complete a comprehensive training programme to prepare him to work for Karl Mayer, which will involve taking part in a course held by the company’s own Academy and going out on service calls with experienced colleagues.
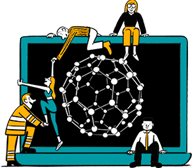
Business intelligence for the fibre, textiles and apparel industries: technologies, innovations, markets, investments, trade policy, sourcing, strategy...
Find out more