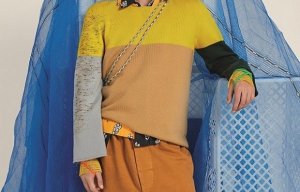
Stoll presents new knit and wear technology
New Stoll patent applied for: Plated Stoll-Knit and Wear® seamless sweater, knit with all needles on the CMS 730 T Knit & Wear with additional beds in the gauge E 7.2 The topic of the new patent applied for is a plated Stoll-Knit and Wear® seamless article knit with all needles in the gauge E 7.2 on the CMS 730 T Knit & Wear with additional beds. The fabric edges appear like seam imitations and have the character of linked seams. They are knitted in purl stitch pattern. Depending on th
14th April 2008
Knitting Industry
|
New Stoll patent applied for: Plated Stoll-Knit and Wear® seamless sweater, knit with all needles on the CMS 730 T Knit & Wear with additional beds in the gauge E 7.2
The topic of the new patent applied for is a plated Stoll-Knit and Wear® seamless article knit with all needles in the gauge E 7.2 on the CMS 730 T Knit & Wear with additional beds. The fabric edges appear like seam imitations and have the character of linked seams. They are knitted in purl stitch pattern. Depending on the material used, the article can be produced either as functional clothing, as active sportswear or as a sporty, colour-plated version for outerwear.
To produce a Stoll-Knit and Wear® pullover, three round fabrics are begun simultaneously, i.e. in the middle the body, and on the left and right the sleeves. The shape of the body piece and the sleeves is realized in accordance with the model during knitting by widening or narrowing stitch groups at the fabric edges or within the fabric pieces by goring. When the underarms are begun, the body is opened on both sides and the sleeves on the respective inner side, and all three pieces are unified to form a round fabric.
The fabric is formed by means of the plating technique, whereby two different yarn threads are fed to each needle. This soon-to-be-patented process enables the ground thread to be reliably covered by the plating thread in the stitches formed with the plating technique. This patent will prevent the errors which frequently occur during the production of plated Knit & Wear articles. The edge areas of the transition from one fabric area to another often show plating errors. One of their causes is that the yarn carrier moving away from the fabric pulls together the stitches of the edge needles, reducing the size of the edge stitches. With these smaller stitches, the ground thread is frequently not covered by the plating thread, and therefore becomes visible. The edge stitches, which then appear to be of a different colour or yarn structure, are then visible as plating errors.
The patent enables a correct alternation of the ground and plating thread at the fabric edges of the Knit & Wear article with the purl stitch technique (see image left). The side seams are imitated by the stitches of the edge area, i.e. purl stitches or purl stitches which alternate by rows with jersey stitches, like those found in conventionally produced knit fabrics. The seam imitation produced with the purl stitch technique feels like the basic fabric and in contrast to seams even if these are very flat, prevents pressure or rubbing spots on the skin. Thanks to the seam imitation, the Stoll-Knit and Wear® article perfectly adapts to the body, ensuring high wearing comfort while emphasizing the aerodynamic shape of the pullover. Of course, purl stitches can also be used as a functional area or as a pattern look within the contours of the sleeves, front or back.
In order to achieve air permeability, but also for design reasons, it is possible to knit a petinet hole pattern in certain partial areas (see image right) or over the surface of the entire Knit & Wear article. Other functional or visual pattern options include single-jersey jacquards, long sized stitches, piqués, lace effect patterns, floating thread patterns, tuck patterns, cast-off patterns, knops, cables etc. These knitting techniques are produced in some cases with the needles alone and in some cases with needles and transfer elements of the machine.
The patent is only possible on the CMS 730 T Knit & Wear with additional beds. As the stitches can be transferred via the additional needle beds, it is also possible to knit the Knit & Wear article with all needles according to the additional-bed transfer principle. Here the use of the additional beds during transfer enables a major reduction in the production times. Shaping is carried out by narrowing with the additional beds without additional transfer rows in a manner favourable to production. Knitting and narrowing are carried out simultaneously in one carriage stroke (see image below). Shaping during fabric processing is carried out by widening individual needles or laterally transferring stitch groups at the fabric edges from the front, back and sleeves via transfer elements. During fabric narrowing, partial areas of the Knit & Wear article are laterally transferred. High productivity is achieved by avoiding empty rows.
The results of so-called body mapping (imaging via the various temperature zones of the human body) play a major role in the development of sports clothing. To exactly adapt the properties of the pullover to the various physical properties of the body, the pullover was divided into different areas. These areas are characterized by the selection of special yarn, or through a special knitting structure, for this patent a petinet pattern. These measures enable optimum results based on the moisture and temperature compensation of the skin.
The special feature of the pullover lies in its shaping. The posture of the cyclist was taken into account by extending the back section of the pullover (see image right). This measure prevents the lower section of the back from cooling down and therefore ensures optimal ergonomic wearing comfort for the athlete.To prevent the sleeves from sliding up, a thumb opening was worked into the sleeve seam and the section for the ball of the thumb was expanded. (see image left).
Consecutive narrowing of the fabric width, fabric edges and imitated seam areas in which stitches are only formed with every second needle and jersey stitches that alternate with purl stitches by rows, plain stitch areas (jersey stitches) on the sleeves and in the front and back, lace effect pattern in the front piece. The knitting techniques are shown in the area of the C-C line and are produced without empty rows.
Business intelligence for the fibre, textiles and apparel industries: technologies, innovations, markets, investments, trade policy, sourcing, strategy...
Find out more