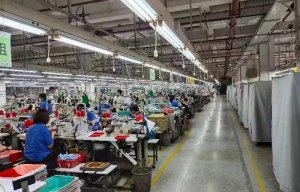
American Phil reaps reward of GSDCost investment
ITMF releases latest International Production Cost Comparison (IPCC).
10th July 2025
Knitting Industry
|
Zurich, Switzerland
The International Textile Manufacturers Federation (ITMF) has released its latest International Production Cost Comparison (IPCC), providing an updated and expanded benchmark for production costs and carbon footprints across the primary textile value chain. This new edition, covering data for 2023, includes for the first time Uzbekistan and a detailed calculation of carbon emissions for each textile product assessed.
The report analyses cost structures for spinning, draw texturing, weaving, knitting and finishing, breaking costs down into individual elements such as labour, power, and manufacturing overheads. One key insight shows that producing one metre of woven cotton fabric in a continuous open width process cost an average of USD 0.94 per metre in 2023, excluding raw material costs. Bangladesh recorded the lowest average cost at USD 0.70 per metre, while Italy topped the range at USD 1.54 per metre.
The data reveal significant regional differences. For example, the spinning stage alone for this metre of finished fabric averaged USD 0.31 per metre worldwide, with a range from USD 0.23 in Bangladesh to USD 0.54 in Italy. Weaving added USD 0.25 per metre on average, while finishing accounted for USD 0.38 per metre, depending heavily on local process efficiency and energy costs.
The IPCC also details spinning costs for NE/30 ring yarn, which averaged USD 1.63 per kilogram globally. Vietnam remained one of the most competitive countries at USD 1.19 per kilogram, whereas Italy recorded the highest cost at USD 2.85 per kilogram. Labour costs, in particular, showed extreme variation: from below USD 0.10 per kilogram in Egypt, Indonesia and Bangladesh, to nearly USD 1.00 per kilogram in Italy. Power costs added further divergence, with the highest in Central America and Italy and the lowest in Pakistan and Egypt.
For the first time, this year’s comparison includes a full carbon footprint breakdown for woven cotton fabrics finished by continuous open width. India emerged with the highest total emissions, exceeding 12.5 kg CO₂ equivalent per kilogram of fabric. Its intensive spinning and weaving stages accounted for the majority of these emissions. In contrast, Brazil’s textile industry stood out for its relatively low footprint—under 4 kg CO₂ equivalent per kilogram—largely thanks to its renewable energy mix and efficient production processes. Uzbekistan’s inclusion brings moderate emissions figures, signalling potential for improvement in line with best practice benchmarks.
These findings underline the growing importance for textile manufacturers worldwide to improve energy efficiency, adopt cleaner power sources and refine processes in order to stay competitive and meet rising sustainability expectations.
The full report provides extensive detail for different reference products, including NE 30 ring yarn, textured polyester yarn, woven and knitted fabrics, and a variety of finishing processes for cotton and polyester.
Business intelligence for the fibre, textiles and apparel industries: technologies, innovations, markets, investments, trade policy, sourcing, strategy...
Find out more