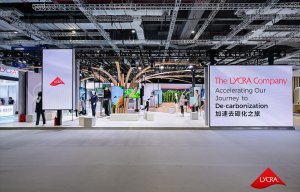
The Lycra Company at Intertextile Shanghai
Opinion
The Journey to Carbon Neutrality at face-to-face Performance Days event in Munich.
6th May 2022
Anne Prahl
|
Munich, Germany
Functional fabric fair Performance Days held its first physical show in over two years from the 27th to the 28th of April in Munich. 186 exhibitors presented their latest collections to 2813 visitors, while the fair’s focus topic investigated ‘The Journey to Carbon Neutrality’ by showcasing fabrics, which demonstrate a reduced carbon footprint through raw material choices, as well as energy-saving measures and resource conservation during production.
Recycled & bio-based synthetics
Polyester is the most ubiquitous fabric in the performance knit sector and the choice for recycled options continues to grow in line with demand from designers and consumers. Compared to conventional polyester, industry figures on the reduction of CO2 emissions vary widely between 20% and 70%, as savings depend on production methods and region, as well as whether the PET feedstock is mechanically or chemically recycled.
3D textures and geometric patterns as well as mesh, birds-eye, waffle and quilted structures featured strongly across recycled polyester base and midlayers. New Wide Enterprise presented an eye-catching collection of technical jacquard double knits in blends of recycled and virgin polyester, as well as 100% recycled polyester.
More suppliers are beginning to consider their fabrics future recyclability by replacing Spandex or Lycra with elasticity by construction. Asahi Kasei utilise a special circular knit construction for their ECOSENSOR midlayer material, while Li Peng Enterprise’s waffle-textured, 4-way stretch is achieved through the use of mechanical stretch yarn. In addition this fabric saves 35% CO2 emissions due to the dyeing process.
As textile-to-textile recycling is still in its infancy, the majority of recycled polyester fabrics are currently made from recycled PET bottles, although textile mills are exploring new sources of feedstock. Warp knit specialist M.I.T.I SPA recently launched their RUBBERMADE by EcoSoul collection, which utilises recycled polyamide made from end-of-life tyres and the company report that 12.4 tyres are used up per 100 metres of fabric produced. This stretch fabric provides UV protection and is suitable for raw cut fabric edges.
Glowtex Innovation presented their Morphlon jersey and terry fabrics, made by mechanically recycling polyester fibres from footwear waste. This approach results in an eye-catching heather effect, which eliminates the need for dyeing. Another company, Men Chuen Fibre Industry, also offer partly recycled polyester midlayer fabric made from footwear material waste. This fabric also boasts mechanical stretch and employs dope-dyed yarn to reduce its CO2 footprint.
Everest Textile’s CCU (Carbon Capture and Utilisation) recycled polyester jersey utilises carbon dioxide emissions from steel mills and petrochemical plants, which are converted into raw materials for polyester fibres. This quick drying fabric provides stretch and is promoted as carbon neutral.
Bio-based synthetics are another interesting area; these types of fabrics are fully or partly derived from renewable resources, such as plant biomass including corn, sugar cane and beetroot. They are often mixed with smaller amounts of fossil fuel-based raw materials to provide durability and additional performance features. New Wide Enterprise combines bio-based and recycled nylon yarn to produce striking three-dimensional jacquard and mesh fabrics, which provide breathability and quick-dry function. The company’s bio-based nylon is made from castor oil, which is able to absorb CO2 emissions during the plant’s growth.
LMA’s fully biodegradable fabric combines biodegradable polyamide with lyocell and cellulosic fibre Naia, made from sustainably sourced pine and eucalyptus pulp in a closed-loop manufacturing process. This soft and comfortable baselayer fabric has a delicate loopback structure and is suitable for lightweight sweatshirts and hoodies.
Plant-based and natural blends
As plant-based fibres have a natural ability to absorb carbon during the plant’s life, much attention was on fabrics made with organic cotton, hemp and Tencel. In addition, there are a growing number of suppliers offering recycled cotton, which reduces CO2 emissions compared to conventional virgin cotton. However, as there are many variables in the manufacturing process, fashion and outdoor industry estimates for reduced impact vary widely between 25% and 80%.
Joaps Malhas presented an extensive range of organic and recycled cotton fabrics and also provide a wide selection of other natural fibres, including hemp, linen, kapok and Tencel. Fabric tactility and functionality can be enhanced through various chemical and physical finishes, all of which are covered by the company’s OEKO-TEX Standard 100 certification.
A. Sampaio showcased the successful use of agricultural waste as a feedstock with two interesting baselayer fabrics. One fabric is an organic and recycled cotton and hemp Agraloop Biofibre blend, while the other is made with organic cotton and banana fibre extracted from waste banana leaves.
Tencel was another pervasive fibre at the show, as it continues to grow in popularity for the use in active sportswear. Due to its use of renewable raw materials and closed-loop production process, the fibre has long been promoted as a more environmentally responsible choice. Lenzing have committed to reaching net-zero emissions by 2050 and steps include the reduction of CO2 emissions through more efficient production methods and using renewable energy resources.
Utenos Trikotazas AB’s hemp, merino wool and Tencel brushed-back midlayer fabric is quick drying and provides thermo-regulation and natural odour protection. Hemp is also known to offer natural antibacterial and UV protection. Due to its sustainability credentials, such as being naturally resistant to disease, minimal water consumption and no need for fertilisers, hemp blends attracted a lot of attention at the fair.
Utenos Trikotazas AB’s aesthetically striking double knit Tencel and polypropylene blend offers thermal regulation, breathability and moisture absorption and is quick drying. Pontetorto Spa offers a 100% Tencel baselayer knit, which is finished with Polygiene OdourCrunch Stays Fresh technology to provide anti-odour properties. In addition, the fabric has a high UV protection factor and is promoted as CO2 neutral.
Wool-based functional fabrics continue to grow in popularity, despite causing high levels of greenhouse gas emissions during the raw material phase. However, wool-based products perform much better when assessed over their entire lifecycle, as they require less washing and tend to last much longer than synthetic products. In addition, wool provides thermal regulation, odour resistance and antibacterial properties and is biodegradable and recyclable at end-of-life.
In order to reduce wool-based products’ levels of greenhouse gas emissions, many suppliers are blending wool with recycled polyester, which also adds fabric durability. Evertex’ Janerino hybrid wool baselayer collection possesses anti-odour characteristics, while thermo-regulation helps the fabric to keep the wearer cosy and warm, enabled by a raised knit texture on the skin side of the fabric.
Popular wool blends for midlayers and fleece-type products include wool combined with Tencel, organic cotton, recycled polyester and recycled polyamide.
Low impact dyeing solutions
Conventional fabric dyeing requires significant amounts of energy and, together with finishing, is considered the highest impact phase during manufacture. As a result, we are seeing a significant growth in colouration technology innovation, including waterless, spun or solution dyeing, also known as dope dyeing.
Eclat’s 100% recycled polyester fabric is produced with recycled solution dyeing, a technology, which melts the rPET chips together with the colour pigments during the spinning process to create vivid and durable colours.
SHEICO’s combination of 58% recycled polyester with 42% dope-dyed polyester produces an appealing tie-dye pattern, while Jersey Lomellina’s NAIR BLACK LINE is made with dope-dyed black yarn to offer extremely high colourfastness.
Hung’s Fortune’s single jersey baselayer is coloured through a low-temperature dyeing technology, utilising ESY (Energy Saving Yarn), which produces vibrantly coloured yarns using half of the energy compared to traditional yarn-dyeing.
Most of these low energy dyeing technologies are only suitable for synthetic fibres, while NEXTIL GROUP’s Greendyes process can be used on a wide range of materials. These include natural and biosynthetic cellulosic, protein-based and recycled polyester and polyamide. The company’s process only utilises raw material of natural, mineral or vegetable origin and, due to being a cold procedure, has extremely low energy consumption.
The fair’s focus on ‘The Journey to Carbon Neutrality’ provided a much-needed impetus to include the fabric’s CO2 impact in the designer’s decision-making process when selecting and developing new fabrics. However, it is important to consider that subject to material and product, an even bigger impact can be associated with washing, tumble-drying and ironing. In addition, any savings made through responsible fabric selection can be wiped out by air freighting products, while designing products for an extended, active lifespan and designing for recyclability at end-of-life, can reduce a product’s overall CO2 impact dramatically.
Business intelligence for the fibre, textiles and apparel industries: technologies, innovations, markets, investments, trade policy, sourcing, strategy...
Find out more