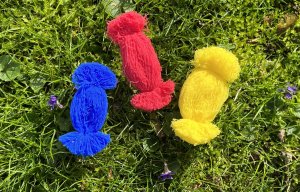
Towards an increasingly sustainable textiles industry
New approach covers yarn pre-treatment and knitting technique to achieve aesthetics that resemble the wash-down effects of traditional dyeing.
19th July 2023
Knitting Industry
|
Lenzing, Austria
Lenzing Group, a leading global producer of wood-based specialty fibres, has introduced a new approach that covers yarn pre-treatment and knitting technique to achieve aesthetics that resemble the wash-down effects of traditional dyeing in ready-to-wear and knit garments.
To address the pollution caused by dyeing and finishing in the textile industry, the new approach will significantly reduce environmental impact and is said to be ideal for use on pre-treated fabrics and yarns made with Tencel Lyocell fibres. The approach also complements the wet-processing and production facilities of fabric mills, bringing added benefits for value chain partners.
One-step dyeing process
In traditional dyeing, multiple washes using a significant amount of water, energy and dyes, and chemicals may be required to achieve a designated shade of colour. With the new approach, only one round of dyeing is required, reducing water, energy and chemical usage by up to 50%, 40% and 90% respectively.
“As consumers become more conscious of the environmental footprint of their purchases, designers and manufacturers are seeking innovative ways to ensure that the materials and production processes deployed have a low environmental impact, while expanding design possibilities,” said Rex Mok, Vice President of Fiber Technical Marketing and Development at Lenzing.
“Our new approach can create wash-down aesthetics or vintage looks on any knit fabric without water-intensive bleaching processes. By overcoming the limitations of traditional dyeing, our new approach is a resource-efficient alternative that helps translate into greater
sustainability and more competitive operational costs for fabric mills. We will continue to work with mill partners to drive wider adoption of the new approach and explore new applications within the textile value chain.”
Unleash unlimited design possibilities
With the new approach’s direct application to Tencel Lyocell fibres or Tencel Lyocell with Refibra technology, different shades of colour, wash-down or fade-out effects can be customised. This makes it ideal to produce ready-to-wear, knit apparel and denim-looking garments in various colour shades.
Existing regular, organic, or natural dyes used by yarn makers and fabric mills are compatible with the new approach. As yarn and fabric processed with the new approach do not leave dye residue on machines, the same machinery can be used continuously for the production of fabrics or garments of different colours. With machine down-time being minimised when changing colour lots, production delays will be shortened, allowing yarn makers and fabric mills to save costs while enhancing production efficiency and sustainability.
Business intelligence for the fibre, textiles and apparel industries: technologies, innovations, markets, investments, trade policy, sourcing, strategy...
Find out more