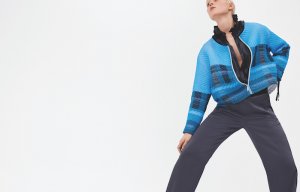
Preview of Stoll's latest Trend Collection
Leading German flat knitting machine builder Stoll has exhibited a new prototype version of its best selling CMS 530 compact flat knitting machine which is faster and better than its predecessor. The CMS 530 multi gauge, with a working width of 50 inches (127cm) and three knitting systems was shown in three different gauges demonstrating three different applications at ITMA Asia. A prototype CMS 530 multi gauge machine was exhibited in 8.2 gauge which according to
5th August 2008
Knitting Industry
|
Shanghai
Leading German flat knitting machine builder Stoll has exhibited a new prototype version of its best selling CMS 530 compact flat knitting machine which is faster and better than its predecessor. The CMS 530 multi gauge, with a working width of 50 inches (127cm) and three knitting systems was shown in three different gauges demonstrating three different applications at ITMA Asia.
A prototype CMS 530 multi gauge machine was exhibited in 8.2 gauge which according to Stoll gives productivity increases of up to 14% depending on the fabric width, gauge and fabric type knitted. This is achieved through different technical improvement measures such as shorter carriage stroke, faster carriage turn around and higher carriage speed. Stoll emphasize that this can be achieved without compromising machine reliability or stitch appearance. The machine’s maximum knitting speed is 1.2m/s but it runs at 1.5m/s on empty rows.
The 8.2 gauge machine exhibited was knitting a men’s fully-fashioned zig- zag offset intarsia front panel sequentially in gauges 12, 14 and 16. (picture 2). With Stoll’s latest intarsia kit fitted to the CMS 530 it is possible to use 32 intarsia yarn carriers (picture 3) in narrow staggering and to supply them individually by means of Stoll’s clamping and cutting devices with 2 x 16 individual clamping and cutting points. This way complex intarsia patterns and 3-colour Jacquards can be produced in a quick and competitive manner, Stoll claims.
A CMS 530 multi gauge in 7.2 gauge was also exhibited with which Stoll demonstrated that permanent analysis of the main machine components is carried out on an ongoing basis. An example of this is in the stitch formation area, where Stoll continues to develop stitch appearance and spectrum and thus also the flexibility of the machines. With the exhibited machine, also a prototype, development was carried out on needle bed geometry, which lead to even higher fabric tension. This was demonstrated by the fabric shown at the exhibition, a sleeveless ladies’ shirt with V-neck and inclined running stitches in split technique without empty rows.
Stoll also demonstrated a new technique for tying-in ends when knitting intarsia on a CMS 530 in gauge 3,5.2. The machine was knitting a sleeveless multi gauge intarsia men’s shirt. According to Stoll, the new patent pending technique offers clear cost benefits for intarsia knitting, as the time-consuming and expensive manual knotting of yarns can be eliminated. The yarn ends are tied-in to the fabric directly on the machine without extra strokes and loss of time.
When knitting a new yarn, the first knitted stitch is split and then immediately transferred again. This way the yarn is fastened tightly to the old stitch. Additionally, this technique offers the possibility of knitting-in the yarn without a tuck loop and to securely feed-in starting from the first needle. With the standard method, the yarn has to be looped to the colour field border by using tuck loop. Afterwards these tuck loops have to be eliminated expensively by hand.
Additionaly, with some yarns it is impossible to avoid visible markings in the fabric. Other knitting-in techniques such as locking by transferring or knitting-in with draw thread can also cause permanent markings. With Stoll’s new split technique the yarn is pressed into the needle hook by the closing needle latch (latch turn over). A secure yarn insertion without markings in the fabric is therefore ensured.
Business intelligence for the fibre, textiles and apparel industries: technologies, innovations, markets, investments, trade policy, sourcing, strategy...
Find out more