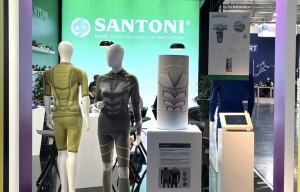
New selective terry options with Santoni SM8-TOP2ST
The precision that we have come to expect from leading flat knitting machine builder Shima Seiki, has now been applied to the company’s Air Splicer, a proprietary device which ensures high quality colour changes in multi colour knitwear. The Air Splicer has been developed for multi-colour knitting on the company’s range of complete garment knitting machines and it is set to significantly enhance the company’s Wholegarment technology. KnittingIndustry.c
14th June 2009
Knitting Industry
|
Carluke, Scotland
The precision that we have come to expect from leading flat knitting machine builder Shima Seiki, has now been applied to the company’s Air Splicer, a proprietary device which ensures high quality colour changes in multi colour knitwear. The Air Splicer has been developed for multi-colour knitting on the company’s range of complete garment knitting machines and it is set to significantly enhance the company’s Wholegarment technology. KnittingIndustry.com was recently invited to view the latest version of Shima’s latest innovation and found the technology to be very impressive indeed.
Although stripes, intarsia designs and certain jacquards can be knitted on complete garment knitting machines there are limitations due to the way that garments are knitted in tubular format, which makes yarn carrier movement and positioning complex, leading to excessive carriage movements and therefore time consuming knitting. Striped complete garments are knitted but there is a need to knit waste at the sides of the garment which is wasteful and time consuming and requires hand finishing after knitting. Complete garments therefore are predominately single coloured, as is most knitwear, but stripes and multi colour garments have been popular recently and Shima’s Air Splicer aims to allow knitters to cope with such fashion changes and demands.
Shima’s Air Splicer, unlike conventional knotting systems which mechanically tie together yarn ends, actually cuts and then twists yarns together with a burst of compressed air with split-second accuracy. Working in precise coordination with the company’s i-DSCS, Digital Stitch Control System with Intelligence, the Air Splicer is able to time each splice so that perfect colour changes can occur exactly as programmed, Shima says. Whether it is intarsia or jacquard, border patterns or argyle shapes, designs and patterns can be knit to precise specification and with beautiful results, the company adds.
Air splicing as a technology has been used in the spinning industry for some years but building a device which allows colour changes with ‘needle by needle’ accuracy whilst the knitting machine is operating, is a significant challenge which appears to have been met by Shima and its Japanese development partner Murata Machinery Ltd. The two companies have been jointly granted a number of patents in this field.
According to Shima, when equipped with the Air Splicer option, the company’s SWG-X complete garment knitting machine features two Air Splicers on each side of the machine, mounted above the i-DSCS units. Each Air Splicer unit feeds one yarn carrier and can deliver eight different yarns or colours per yarn carrier. This means that the machine can knit up to 32 colours via 4 yarn carriers under optimum conditions, Shima says. The rest of the yarn carriers are available for additional colours, demonstrating how the Air Splicer realizes dramatic increases in multi-colour production potential.
We recently viewed Shima’s Air Splicer at the company’s Shima Seiki Europe Scottish branch office, which provides sales and service to Scotland’s high quality knitwear industry in the Scottish Borders region. The SWG-X 12 gauge machine we viewed was fitted with two units on the left hand side and one on the right hand side. The left hand side Air Splicer units were controlling the left sleeve and main body colours and the single unit on the right hand side of the machine was controlling the right sleeve colours.
To set up the Air Splicer, the machine needs to know the distance from the splicing point to first needle to be knitted. The Air Splicer knots the new colour with the old colour and the knot is pulled through manually to the designated yarn carrier, whilst the i-DSCS encoder records the amount of yarn required to reach the first needle to be knitted. This operation is carried out for each yarn carrier to be used and the technician records this data on the machine controller for each yarn carrier. In the case of the right hand side splicer, where the yarn carrier is introduced from the right, it is necessary to drag the yarn carrier to the left hand side and the first needle to be knitted, to record the value.
The technician then runs a ‘flexi-start’ before commencing knitting which checks the ‘auto splicer work point make data’ and calculates the yarn requirements for each splice in the data. Otherwise, the set up is the same as with normal Wholegarment knitting but with seven colours plus the base colour for each yarn carrier. When the spliced yarn comes through the yarn carrier tip, the knitting data automatically tells the machine where to tuck in and out, so that the splice sits on the inside of the garment and gets locked in. When the garment is removed from the machine, the knot can be cut and the two different colours are locked into the garment. Each splice takes no more than a few seconds and all cut ends are sucked away to a waste collector at the splicing point.
The first Air Splicer units are now being tested by Shima’s customers and it will allow them to offer multi-colour garments in a very wide range of designs in Wholegarment seamless format, which is a prerequisite for the true proliferation of seamless knitwear technology. This really is a big step forward and the Air Splicer, coupled with the company’s new MACH2 range of high speed Wholegarment machines, points to a knitwear manufacturing future where almost any structure or pattern can be knitted in seamless format cost effectively.
Business intelligence for the fibre, textiles and apparel industries: technologies, innovations, markets, investments, trade policy, sourcing, strategy...
Find out more