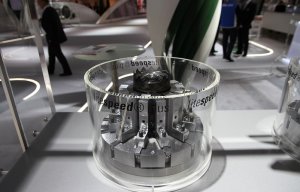
Groz-Beckert’s litespeed plus in action at ITMA Asia
ADVERTISEMENT Direct customer benefits with litespeed ® needles: Substantially reduced carbon footprint Energy consumption and machine temperature reduced by up to 20 % Significant increase in performance Reduced oil consumption due to optimized lubrication litespeed ® - A SMALL DIFFERENCE WITH A BIG IMPACT Main characteristic features of a litespeed ® needle Optimized needle shank geometry due to partial reduction of the needle shank thickness in circular knitting needles Reduced
31st July 2011
Knitting Industry
|
ADVERTISEMENT
Direct customer benefits with litespeed ® needles:
Main characteristic features of a litespeed ® needle
Shank geometry
The drawing above right visualizes the geometry of the litespeed ® needle. The enlarged image shows the partially reduced areas of the needle shank.
This shank geometry makes the needle shaft more flexible, making the needle more resistant to breakage at higher machine speeds.
THE BENEFITS OF litespeed ® AT A GLANCE - FOR EVERY CIRCULAR KNITTING MACHINE
litespeed ® optimizes lubrication behaviour and reduces oil consumption.
The partially reduced needle shank thickness permits improved distribution of the needle oil.
Benefits:
litespeed ® reduces energy costs - permanently!
The lower degree of friction against the trick walls and reduced needle weight make for easier needle movement.
Benefits:
litespeed ® reduces the machine temperature
The speed of modern high-performance circular knitting machines is frequently limited by high temperatures. In practice, in some cases up to 100°C can be generated at the cylinders or cam. By using litespeed ® needles, machine temperatures can be reduced by up to 20 %.
Benefits:
litespeed ® permits productivity increases
Due to the partially reduced needle shank thickness, the litespeed ® needle is more flexible and consequently more capable of withstanding stress. The shock waves caused by the needle butt hitting the cams are more effectively absorbed, significantly reducing the risk of needle breakage.
The combination of lower heat generation, optimized oil distribution in the shank area and improved flexibility of the needle shaft add up to permit higher machine speeds and consequently improved productivity.
0.6 GRAMS OF INNOVATION EQUALS MANY TONS OF REDUCED CO2 EMISSIONS
The above calculations are based on the following parameters:
Single jersey machine PAI LUNG, 34", E 28, 2,988 needles, current consumption per hour at a machine speed of 17 rpm:
Standard Vo 141.41 G 001 1.914 kW
litespeed ® Vo-LS 141.41 G 001 1.616 kW
Average machine running time per day: 15 h
Average machine running time per week: 6.5 days
Life of a needle set (3.000 needles): 4,000 h
CO2 emission factor (electricity mix India): 1.271 kg CO2 / kWh
This enormous reduction in carbon emissions is equivalent to the
following distances travelled by different means of transport:
10,080 km in a modern mid-size car
3,979 km in a plane (Frankfurt - Bombay 6,584 km)
37,801 km by rail
75,602 km by bus
Information on CO2 emissions: 2)
Passenger car: 150 g CO2 / km
Aircraft: 380 g CO2 / km
Train: 40 g CO2 / km
Bus: 20 g CO2 / km
Source: www.CO2-emissionen-vergleichen.de
1) The CO2 emission factor is based on information on the electricity mix in India. Other countries have a different emission factor. Production of the litespeed ® version of 3,000 needles creates 3 kg of CO2. These emissions have been taken into account and deducted in the above calculation.
2) The CO2 emissions specified for the vehicle types relates to a single person.
litespeed ® couples efficiency with energy savings
Groz-Beckert is the proud recipient of the KYOCERA Environmental Award for its pioneering and innovative development of the litespeed ® needle for circular knitting machines.
The KYOCERA Environmental Award is one of the most hotly contested environmental accolades in Germany and focuses on innovation, market potential, environmental benefit and transferability to other companies.
Tests also verify impressive results as regards sustainability: If all the relevant machines around the world were fitted with litespeed ® needles, the result would be an annual CO2 reduction of over 475,000 tons compared to the energy consumption of standard needles.
This overall saving is equivalent to an Airbus A 380 travelling 302 times around the globe with 525 passengers on board.
GROZ-BECKERT KG
PO Box 10 02 49
72423 Albstadt, Germany
Phone +49 7431 10-0
Fax +49 7431 10-2777
Business intelligence for the fibre, textiles and apparel industries: technologies, innovations, markets, investments, trade policy, sourcing, strategy...
Find out more