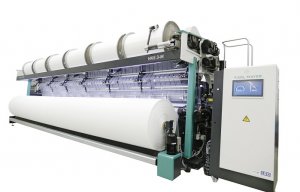
Karl Mayer launches widest tricot machine available
Leader in warp knitting technology, German company Karl Mayer has developed an active pattern beam drive for its high-speed lace machines which consists of a tension controlled yarn delivery system that the company says can be can be used with all pattern beams. Karl Mayer says the innovative control principle has already been used in practice by customers operating its raschel lace machines and the system is based on the tried and tested servo system, which has b
26th July 2010
Knitting Industry
|
Obertshausen
Leader in warp knitting technology, German company Karl Mayer has developed an active pattern beam drive for its high-speed lace machines which consists of a tension controlled yarn delivery system that the company says can be can be used with all pattern beams.
Karl Mayer says the innovative control principle has already been used in practice by customers operating its raschel lace machines and the system is based on the tried and tested servo system, which has been successfully used for many years now for driving the string bars.
A new and improved version is currently being tested and the changes that are incorporated in the improved version relate to the use of a new type of motor and replacing the existing friction control system with toothed wheels for power transmission.
In passive pattern yarn feed, the pattern beams run on ball bearings and are driven by the yarn let-off system at the knitting point, a solution which Karl Mayer says has its limitations at high machine speeds. Despite the use of balancing units, the physically induced mass inertia of the longitudinal shafts, together with the yarn warps which are arranged in a row, is said to be so great that it can cause undesirable changes in the fabric appearance. Acceleration causes distortion, whilst braking results in undesirable compaction. Consequently the system using the pattern beams is limited when higher speeds are required. Creels were used previously to deliver the pattern yarns at higher speeds. However, these multi-position creel systems require a large amount of space and an especially large number of bobbins which are loaded onto them. This is a disadvantage which, in particular, makes pattern development and processing small runs expensive and complicated.
As an alternative, Karl Mayer has now developed a pattern beam with active drive. The new system consists of a sensor for determining the yarn tension in one yarn for each pattern beam axle and a motor system whose speed is controlled on the basis of the results of equalising the target/measured values. In this case, the desired values have to be input in advance. As a result, any fluctuations in consumption are equalised, even at high operating speeds and any mass-induced imbalances are evened out. This means that the balancing units are no longer needed at the pattern beams, but above all, creels are no longer required to deliver the pattern yarns on high-speed lace machines, Karl Mayer says.
Karl Mayer says the product should be ready for launch by the end of this year and will give customers a range of options. Lace raschel machines with creels and pattern beams are still available if required and a retrofitable version for existing machines is also planned.
Business intelligence for the fibre, textiles and apparel industries: technologies, innovations, markets, investments, trade policy, sourcing, strategy...
Find out more