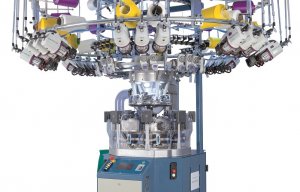
Santoni takes part in Textile Evolution
Part Two of a two part Feature 15 June Last weekend we reported from Santoni Days in Brescia, Italy, that circular seamless machine builder Santoni SpA had shocked the knitting and hosiery industries by introducing a double needle bar raschel warp knitting machine for producing seamless garments with integrally knitted sleeves. In Part 1 of a two part Feature we explained the principles of the development and here in Part 2 we look at the potential for the technology.
15th June 2008
Knitting Industry
|
Brescia
Part Two of a two part Feature
Last weekend we reported from Santoni Days in Brescia, Italy, that circular seamless machine builder Santoni SpA had shocked the knitting and hosiery industries by introducing a double needle bar raschel warp knitting machine for producing seamless garments with integrally knitted sleeves. In Part 1 of a two part Feature we explained the principles of the development and here in Part 2 we look at the potential for the technology.
In Part One we gave a brief explanation of how a seamless garment is created on the SDW8. Some readers familiar with flat and circular weft knitting but not warp knitting asked for further explanation and so we repeat details of the knitting process below and have included a diagram for further clarity.
Each SDW8 machine is fitted with two opposing needle bars equipped with compound needles which are fed yarns by moving guide bars. Warp yarns are selected via the electronic selection system via piezo elements, and presented to those needles which are to be knitted.
For a seamless garment, knitting commences with the knitting of three tubes (1) side by side (sleeve/ body/ sleeve), which are created by knitting on both needle bars and by closing each tube at the edges by knitting. Knitting then continues to the underarm position at which point knitting proceeds in a single tubular fashion (2) up to the neck opening. However, the shoulder shape of the garment is created by joining of the knitting of both needle bars in a predefined pattern within the tube (3).
When the neck opening has been reached, the cycle starts over again to commence knitting of the next garment (4). To convert the lengths of body blanks into garments, the waste sections are removed by cutting and the shoulder line which was created by joining the knitting of both needle bars, acts as a seam. Each garment blank is separated from the other by a simple horizontal cut. To produce a garment with short sleeves, the sleeves are cut to length and seamed subsequent to knitting.
As well as seeing the SDW8 as a tool for simplifying the manufacturing of seamless garments, Lonati Group sees the development as an exciting new opportunity for its existing customers.
Group spokesperson Franco Sciacca told Knitting Industry: “We have been telling our Seamless and hosiery customers who have visited the show, that they now have to think of the SDW8 as a mini garment knitting factory. They have to think of themselves as garment producers who can switch from outerwear such as sportswear to lingerie to hosiery at will.”
This does seem quite feasible. Hosiery manufacturers accustomed to producing on say Lonati or Sangiacomo circular hosiery machines could install an SDW8 machine in a corner of their factory (it uses around six square metres of space) to start producing outerwear such as sportswear. The company could buy yarn on 21 inch beams from a commission warping operation and then send its garments out to a garment finisher. When the sportswear order has been completed the machine could then be switched to produce say fancy hosiery.
For smaller producers the implications are that they need to hire a warp knitting specialist to programme and put the machine into production. They would buy their yarns on beam instead of yarn package and they would send their garments to a finisher as normal. But they could offer a much wider range of products to their customers.
For larger producers the implications are similar in that they need a warp knitting specialist. Some vertical operations already using Santoni circular seamless will have warp knitting capability in-house.
This brings us to the issue of who is going to supply double needle bar raschel technology for producing seamless garments. Franco Sciacca, explained: “Santoni Seamless is known by all of the world’s major brands in intimates, sportswear and activewear and knitted outerwear. We have around four hundred customers worldwide producing seamless garments on our circular knitting machines. Other double needle bar raschel knitting machine builders, who are introducing seamless garment knitting, are traditionally sellers of machines to fabric manufacturers who in turn sell their fabrics to garment producers.” Sciacca added: “At Santoni, we and the rest of the Lonati group sell machines to garment manufacturers, whether that is for socks, pantyhose or lingerie or sportswear. We have a receptive customer base who are garment manufacturers and direct access to the major brands.”
Santoni seamless garments are knitted on body size machines circular knitting machines which are typically 10 – 24 inches in diameter. The machine knits a tube and imparts shape to the garment by varying the stitch length and or the stitch structure. Many Santoni garments are sleeveless as they are used in intimates. Where sleeves are required such as in sportswear, sleeves need to be knitted separately on the same machine or a similar machine and are attached by sewing after the knitting process.
This is achieved through a cutting and sewing process where tubular fabrics are slit and then cut to shape to form sleeves which are then sewn into the body tube to make a garment. This is both labour intensive, although Santoni have automated to some extent, and wasteful, as something like 30% of the fabric is thrown away. With Santoni’s new SDW8 warp knitting machine, the sleeves are knitted integrally and although there is some cutting waste, around 10%, labour involved in the cut and sew operation can be reduced.
The real potential for Santoni’s SDW8 is in market segments where garments are required to have sleeves. There is a clear advantage for the manufacturer who can reduce production costs whilst being able to offer the customer something extra. There is also an advantage for the brands that can extend the seamless concept into long sleeved garments for sportswear and activewear as well as other knitted outerwear.
The SDW8 is a double needle bar raschel knitting machine equipped with eight guide bars with a working width of 44 inches (1118mm). Two versions of the machine were shown at Santoni Days in 24 gauge (needles per inch), each of which was knitting two seamless garments side by side in chain formation, with garment blanks to be separated later by cutting. A women’s long sleeved top was being produced which required some cutting but no sewing except for the addition of trims if desired.
Visit Knitting Industry regularly for further updates.
Business intelligence for the fibre, textiles and apparel industries: technologies, innovations, markets, investments, trade policy, sourcing, strategy...
Find out more