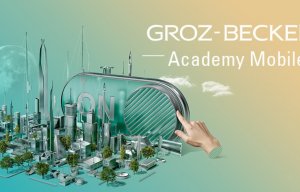
Groz-Beckert July seminars
With new features, the k.management dashboard offers even more support for day-to-day work.
2nd March 2022
Knitting Industry
|
Obertshausen, Germany
Trade conflicts, supply chain bottlenecks and increased competition are leading to enormous cost pressures on producers worldwide, including warp knitting companies, and only those who use their resources optimally can survive, says leading machine builder Karl Mayer.
The German company’s tech subsidiary KM.ON has developed the k.management dashboard to enable manufacturers of warp knitted textiles to fully exploit their potential.
The smart tool uses near-time data from warp knitting machines connected to the KM.ON Cloud via k.ey to provide an overview of key figures, anytime, anywhere. The practical dashboard was launched in 2018. This was followed by continuous optimisations in cooperation with pilot customers, including Filesan.
Up to 15 employees from the Turkish manufacturer of warp knitted net fabrics – principally designed for agriculture – used the k.management offer for production planning and quality control purposes, while CEO Bilgin TürkoÄŸlu was also constantly connected to production events.
“I saved the link I needed at the time to my Google favourites. The dashboard was running constantly in the background. I checked the figures almost hourly,” explains the Managing Director, who until then had to call the Production Manager for further details every time the machine stopped for a longer period of time. While the dashboard is a useful tool for him, there is still room for improvement based on his feedback.
Input from Filesan and all other pilot customers led to an initial upgrade in March 2021 and further optimisations followed in October 2021. The latest generation dashboard now offers even more transparency in production with new functions, and therefore provides the basis for highly efficient management of all resources and processes.
“The machine situation remains unchanged, but customers can act proactively and promptly, by optimising how employees are scheduled for example,” explains Marcel Wenzel, Product Owner at KM.ON. “No one has to routinely check the situation on the machines anymore.”
Detecting problems at a glance
To ensure highly efficient production, manufacturers of warp knitted textiles must avoid unnecessary, costly interruptions. Upcoming steps have to be planned in advance and real-time information has to be provided quickly. This is precisely what the k.management dashboard offers.
The tool provides a live overview of all machines that is available anywhere, highlights problems such as machine downtime using easy-to-understand symbols and also suggests the cause. Rapid detection makes efficient intervention possible, which allows customers to optimise their delivery reliability, machine utilisation and machine downtimes, all while maximising yield.
Sorting by activity pressure
To maximise machine utilisation and thus profitability and delivery reliability, a special sorting function has also been integrated into the k.management dashboard. The feature shows the next planned machine stops and any unplanned down-time. Planned service interruptions occur, for example, due to beam changes and are sorted based on urgency.
Unscheduled stops are triggered by things such as a yarn break and are immediately recognisable thanks to the machines being ordered and grouped according to status.
By providing information about the upcoming measure at an early stage, resources can be used optimally: it is always clear which employee has to look after which machine and when, therefore meaning production runs as efficiently as possible.
Looking to the past to efficiently plan the future
Another challenge for warp knitting mills is the pressure to optimise their processes. Production processes must be extremely lean and cost-efficient. The k.management dashboard supports this via a function that displays the status history – running, stopped, offline – of each machine to date. When conducting a review, the maximum time span is three months. Based on the chronology, the value-added contribution of each machine can be analysed in detail and compared with other machines to optimise important work processes.
Moreover, shift changes can be facilitated. As part of this process, answers to key questions about what happened during the last shift are handed over as well as the tasks. Features are currently being prepared for this, which relate to the frequency and type of production fault, the cause and time of a machine failure, the duration until machine operation is resumed or the causes of performance differences between machines.
Business intelligence for the fibre, textiles and apparel industries: technologies, innovations, markets, investments, trade policy, sourcing, strategy...
Find out more