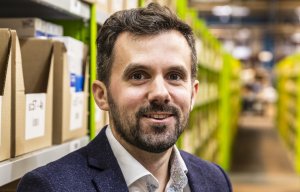
Retailers toughening up on taking back
Circular knitting machine builder Mayer & Cie. is only too aware of the pressures faced by its customers, especially in these troubled economic times. Here, the German company talks about its technological efforts to help its customers ease some of the cost pressures they face and retain competitive advantage. “Faster, further, higher” – time is marching on at an ever faster rate, and with it the speed of technical progress. As a new day dawns, yesterday’
6th May 2009
Knitting Industry
|
Albstadt
Circular knitting machine builder Mayer & Cie. is only too aware of the pressures faced by its customers, especially in these troubled economic times. Here, the German company talks about its technological efforts to help its customers ease some of the cost pressures they face and retain competitive advantage.
“Faster, further, higher” – time is marching on at an ever faster rate, and with it the speed of technical progress. As a new day dawns, yesterday’s latest ultra-new development is already old news. Technological progress for its own sake? No, quite the contrary.
Globally networked markets and state-of-the-art communication technologies create greater transparency and highlight alternatives. Competition is no longer all about the big versus the small, but about the fast beating the slow. Those who lose no time in making selective use of new technologies to conquer their market stand to make substantial competitive gains in terms of performance, of quality and, most importantly, of price.
There is no more cost-effective method to manufacture fabrics than circular knitting. As this realization has long since been shared by producers around the world, the competition amongst circular knitting factories is understandably enormous. Whether mass producers or specialists in niche markets, achieving high output and the best possible quality are paramount. And all at the most favourable possible price. Or put another way: Expectations are on the increase while prices are in decline.
Consequently, successful circular knitting producers today have every cost worked out down to the last cent. The dual factors of production costs and quality have become decisive to survival, and are closely linked to choosing the right production facilities. The essential criteria here are performance and reliability, the greatest possible machine availability and outstanding quality in the finished fabric.
Any producer capable of supplying the same quality at a more favourable price or better quality at the same price is in business, but by the same token, those able to offer both higher performance and better quality have an unbeatable advantage.
An old adage in business that “the profit is in the purchasing” suddenly takes on a whole new meaning. The amount invested is no longer the yardstick in any purchasing decision, but the opportunities offered for fast payback by optimum capacity utilization, a high turnover and consequently healthy profits.
As the market leader in the circular knitting machine sector, here too Mayer & Cie. has a decisive edge over its competitors. Working on the premise that “forewarned is forearmed”, the company’s development team has come up with machines permitting outstanding speeds, for instance of up to 2 m/s in continuous operation in the field of single jersey production, without compromising the legendary Mayer & Cie. quality standard. Speeds achieved include for instance 50 rpm (Relanit 4.0) or 45 rpm (Relanit 3.2 II) with a 30 inch diameter.
The conditions for not only achieving this high level of performance but also its reliable utilization in continuous operation could not be more ideal at Mayer & Cie. It is only through the use of relative movement technology, which benefits from fewer deflection points in the stitch-forming area for optimum care of the yarn, that speed factors (rpm x diameter) of up to 1,500 can be reliably achieved in continuous operation.
Mayer & Cie. was responsible for developing relative movement technology to the series production stage, and implementing this revolutionary new method in its Relanit machine series. Extensive expertise gathered over almost two decades, both during in-house further development work and also from practical hands-on experience with over 7000 sold Relanit machines, has fed into the development to this high-speed technology.
Another technology which key to the achievement of these outstanding performance levels is represented by the three letters MCS: The Mayer Cleaning System is a patented Mayer & Cie. development which is as simple as it is ingenious: While the principle is simple, the effects are astounding.
A channel is created around the knitting head by openings made in the segments through which air is blown. This does not require the use of expensive compressed air, but simple room air at no cost. The air is channelled by a fan and forced through side channel compressors.
The passage of air also exerts a beneficial cooling effect in the stitch-forming area. The cleaning effect is achieved by the air being forced upwards out of the system. Lint is largely kept away from the stitch-forming area, and existing dirt in the cam and needle areas is carried away.
Practical experience has shown that MCS can extend the service life of needles by up to 200% depending on the yarn type used. Oil consumption is also significantly reduced, cleaning cycles are extended and fewer machine repairs are required.
This claim applies figuratively to all high-speed machines, but it is also true in the literal sense too. Mayer & Cie. circular knitting machines have always been characterized by their outstanding stability and torsional rigidity. Because a firm footing is an essential factor in ensuring production reliability and end product quality, the familiar Mayer & Cie. frame design has been further reinforced for the high-speed machines.
Mayer & Cie. has developed its own braking system specifically for the high-speed machines. Guaranteeing gentle, absolutely jerk-free braking, the electronically controlled Process Controlled Brake (PCB) system is provided as a standard feature.
With an hourly production output of 60 kg and over, reliable yarn delivery takes on a whole new significance. Knitting-on aids which knit on at the press of a button, servomotors for automatic tape control, and ceramic yarn feeders offering unique dimensional accuracy and smoothness are just some examples from a whole catalogue of measures to fine-tune all the machine components for extreme output in continuous operation.
The increased use of modern synthetic fabrics and the growing significance of elastomer plating have made open-width technology increasingly an essential part of a knitting factory’s standard equipment outfit. It was a logical next step to adjust the output of open-width frames in step with the speed of the new high-performance machines.
Mayer & Cie. offers open-width frames capable of speeds of 40 rpm in continuous operation (30 inch diameter, fabric width from 2,200 to 2,300 mm), both for mechanical and electronic circular knitting machines, permitting a production increase of 25% over conventional frames with speeds of 32 rpm.
Development work to enable this outstanding performance increase included improvements to open-width takedown systems and inverters, a complete redesign of the drive systems, software modification, and reinforcement of bearings and the integration of a speed-controlled braking system. The development team working on the high-speed frames benefited from the outstanding stability of the frame construction which has always been a characteristic feature of Mayer & Cie. open-width frames. The new high-speed open-width frames can be used on all Mayer & Cie. circular knitting machines with corresponding output.
Business intelligence for the fibre, textiles and apparel industries: technologies, innovations, markets, investments, trade policy, sourcing, strategy...
Find out more