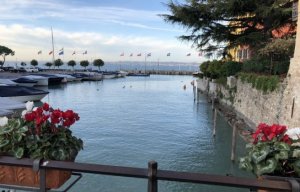
A.DI.CI chief re-elected
Editor’s View
Knitting Industry recently visited a number of producers in the area around Castel Goffredo to find out if the ‘district’ was still in fact world class.
12th September 2019
Billy Hunter
|
Castel Goffredo, Italy
Castel Goffredo, situated in the province of Mantua, in Lombardy close to Lake Garda, is a centre of expertise in the production of woman’s hosiery. © Knitting Industry
Castel Goffredo is situated in the province of Mantua, in Lombardy, Italy. The town and surrounding district have been involved in textile production since medieval times but during the 20th century the area became a centre of expertise in the production of women’s hosiery and is known internationally for its quality and inventiveness both in terms of product and business innovation.
Knitting Industry recently visited a number of producers in the area around Castel Goffredo to find out if the ‘district’ was still in fact world class and to try to gauge how it is evolving to compete in the now globalised and highly competitive hosiery industry. The first article in our series looked at two companies who have reinvented themselves, having started life as private label manufacturers for the big brands and retailers. You can read the full story here - Castel Goffredo: World class hosiery manufacturing centre.
Our second article in the series, looked in detail at the make-up of the Castel Goffredo hosiery producers – the products they manufacture, and where they sell their output. You can read the full story here - Castel Goffredo: World class hosiery manufacturing centre - Part II. In the third article in the series, we profiled more companies and looked at more Castel Goffredo innovations – including new technologies, product and process innovations, and innovative business models. You can read the article here – Castel Goffredo: World class hosiery manufacturing centre - Part IIl.
In this fourth article in the series, we look at two more companies that are breaking the mould – a family owned hosiery manufacturer, which is internationalising its business, developing its own brands and growing its online footprint via e-commerce, and a world class dyehouse that is critical to the future success of the Castel Goffredo hosiery and seamless cluster.
We head to Castel Goffredo to visit Calzificio Schinelli Srl., a family owned company that has been in business since 1960. With a handed down Made in Italy tradition run by a third generation, Schinelli is a family story that is based on research, innovation and industrial organization. Owner-manager Marco Schinelli has been running the company with his wife and two sons, since his father retired 15 years ago.
Owner-manager Marco Schinelli. © Knitting Industry
The company's strengths are a technologically advanced plant, the high quality that distinguishes its products and its experience in the private label business. In order to respond rapidly to market needs, Calzificio Schinelli offers several collections of classic and fashion hosiery.
At the heart of the company is a large manufacturing unit covering around 8,000 square metres. Schinelli’s so called ‘technological laboratory’ houses a plant of 200 or so modern Matec and Lonati hosiery, seamless and socks knitting machines, which are managed by a highly skilled team of professional technicians and operators. The company runs a ‘100% Made in Italy’ business with yarns supplied by local hosiery specialist Fulgar and others, and dyeing and finishing services procured from Tintoria Maniffatura Barbara, based in a nearby village.
Calzificio Schinelli’s capacity is 70,000 pairs of tights per day or 15 million pairs per annum.
The company offers a wide range of products made with special yarns for the most demanding tastes - from cooling products for summer, to its anticellulite and sustainable lines.
Schinelli’s so called ‘technological laboratory’ houses a plant of 200 or so modern Matec and Lonati hosiery, seamless and socks knitting machines, which are managed by a highly skilled team of professional technicians and operators. © Knitting Industry
Schinelli makes for the premium hosiery brands - 70% of turnover is from private label manufacturing and the other 30% is made up of own brand and e-commerce, and it's the latter two areas where Marco Schinelli sees the company’s future.
Marco Schinelli is on a mission to internationalise his company. “The market is currently quite poor, but we are still investing. Our new strategy is multi-diversification, where we will continue to develop our own brands and our e-commerce business. The margins in these areas are good whereas with the private label business, the margins are low. The quantities in the private label business are also now much lower than before – some years ago you needed five customers, now you need fifty customers,” he explains.
Calzificio Schinelli’s 8000 square metres factory in Castel Goffredo, Italy. © Calzificio Schinelli
E-commerce and the Amazon factor
E-commerce is definitely a hot topic at Schinelli – it has doubled in size every year for three years and now constitutes 15% turnover – with 90% of that 15% coming from Amazon sales and 10% from the company’s own online brand Calzitaly. The company was one of the first hosiery manufacturers in the district to go into e-commerce.
Marco Schinelli has set up a commercial venture in New Jersey, USA to enable it to deal with the giant Amazon online retail organisation. Sitting in Marco’s office, there is a real buzz about the place with workstation bound millennials beavering away and darting in and out of various offices. Schinelli’s US customers are Amazon Prime, where it makes for Amazon’s stock, and the Amazon Seller programme, where hosiery is shipped directly to the consumer by Schinelli.
Schinelli also sells through its own B2B website where the minimum order is EUR 150.
It also owns the Belgian Cette brand, a high-quality hosiery brand which the company acquired through a historical connection. “The curvy market is also moving, and we invest a lot in that area – Cette has a good curvy range,” Marco says. The company is currently trialling a new 4 ½” 430 needles Lonati machine for bigger sizes like XXL.
Calzitaly
“Today we need a to offer a stock service. We have six people working in our Calzitaly business. We have tight computerised stock control and we have multi lingual staff in customer service staff, packaging and product information and we are still developing. This is a business which is much more complex to manage as Calzitaly is direct to consumers,” Marco Schinelli explains.
“Calzitaly is an innovative project born from the long tradition of Calzificio Schinelli and realised to explore the new world of e-commerce. A website built for a fast and comfortable shopping experience is at the project’s core and is, the perfect bond between tradition and innovation.”
Gold Collection by Calzitaly. © Calzificio Schinelli
The Calzitaly Gold Collection is an exclusive product line, which aims to take the high quality of Made in Italy worldwide, is a ‘refined collection for the most sophisticated and elegant tastes.’ The Curvy Collection is a new product line by Calzitaly that has, according to the company, been designed especially for ‘the softest beauty – a wide range of products which shapes and contains the curves.’
Curvy Collection by Calzitaly. © Calzificio Schinelli
Schinelli is currently modernising its 200 strong knitting machinery plant and has replaced 32 machines very recently, with the latest models from leading Italian machine builder Lonati.
Leaving Castel Goffredo, we drive south for 10 minutes to visit a company which plays a very important part in the district’s hosiery industry. Tintoria Manifattura Barbara Spa is a leading company in the dyeing and finishing of hosiery and underwear, based in the small town of Castelnuovo di Asola.
Tintoria Barbara, Castel Goffredo, Italy. © Tintoria Barbara
Tintoria Barbara was founded in 1968 and today has a workforce of around 80 employees. It is considered a ‘point of reference’ in the district’s hosiery and knitted goods industry. The company dyes a wide range of natural and manmade fibres and processes around 400,000 pairs of tights and 20,000 pieces of seamless underwear per day, in a modern 10,000 square metres dyehouse.
But it’s not about quantity here - quality is of paramount importance. “Not only quantity but also quality – everything is checked twice. The colour must be solid - a third control,” Tintoria Barabara’s laboratory manager tells me.
Tintoria Barbara is the go-to place for dyeing and finishing for producers of pantyhose and seamless goods in the Castel Goffredo area – it is an important part of the cluster’s infrastructure.
The company’s mission is to satisfy the multiple needs of its customers in the development and improvement of their products, whilst offering assistance that starts from sampling and ends with the finished garment. Attentive to the needs of the market, the company combines research and development and is constantly searching for new application techniques to achieve the quality finishing standards the market demands, in compliance with the health and environmental protection regulations in force.
Tintoria Barbara is totally independent energy wise and has invested heavily in sustainable technologies. The company uses an ECOMAX co-generation system which is made in nearby Brescia.
Purifying effluent at Tintoria Barbara. © Tintoria Barbara
Cogeneration refers to the process where both heat and electricity are obtained from the same fuel (gas in the case of Tintoria Barbara) at the same time. The heat energy from the system is also used directly, as heat, or indirectly to produce steam, hot water, and hot air, thus making it a CHP or cogeneration system.
“Around 500KW is generated by photovoltaic solar panels and another 600KW is generated by co-generation – by gas - also works water,” the company says. “However, as the cost of gas going up, we are reconsidering.”
“We are investing heavily in sustainability and are also part of a project with the University of Trento regarding more advanced sustainability. We are using colours with fewer heavy metals.”
“After dyeing, when the water is cleaned it cannot be used in the normal water system, as is too clean - and we would have to pay tax. But the hot water can be used for the co-generator and the wastewater used in agriculture.”
In order to protect the final consumer, since 2007 the company has certified its service according to Oeko-Tex Standard 100. “This certification is an indication of a human-ecological quality of textile products and of the work done to obtain the best possible result,” the company explains. “Now, we are going for Oeko-Tex Green – the top level.”
The company dyes a wide range of natural and manmade fibres and processes around 400,000 pairs of tights and 20,000 pieces of seamless underwear per day, in a modern 10,000 square metres dyehouse. © Tintoria Barbara
The Made in Green by Oeko-Tex label verifies that an article has been tested for harmful substances. This is carried out through certification in accordance with Standard 100 by Oeko-Tex. It also guarantees that the textile product has been manufactured using sustainable processes under environmentally friendly and socially responsible working conditions. This is carried out through certification in accordance with STeP by Oeko-Tex.
With Made in Green, consumers can use a unique product ID on the label to trace the countries and production facilities in which the labelled article was produced.
Laboratory
Tintoria Barbara’s laboratory is equipped with a Rotarch colour lab built by Salce in Biella. The fully automatic colour lab has three towers, each of which can hold up to 5000 recipes. The specially built machine stores each newly created colour in its archive, with each cartridge holding a piece of dyed fabric.
“The professionalism and experience of our technicians combined with the use of advanced machinery, allow us to offer our customers a valid support in the study and development of samples,” the company says. “The reproduction of the requested colour takes place through the instrumental reading of the desired tone and the use of equipment that allow the creation of small quantities.”
© Tintoria Barbara
The development of new products takes place through the study and research of specific raw materials and auxiliaries and yarn tests in standard or customized dyeing baths. In addition, Tintoria Barbara offers a customer support service to evaluate the dyeing process suitable for best enhancing its products in terms of quality and cost. The technical staff of the laboratory performs the solidity tests to verify the quality standards required by the customer.
Dyeing
In its dyehouse, Tintoria Barbara has invested heavily in modern equipment and has a wide array of different types of machinery, to allow it to be able to respond positively to the requests of its customers.
For example, it has: 20 dyeing cabinets, with capacities ranging from 20kg to 300kg, suited to dyeing items which have already been fixed or ironed; 4 circular machines with different capacities from 170 kg , ideal for the dyeing of crumpled material; 7 rotary machines for dyeing seamless items and pantyhose, in natural fibres such as cotton, wool, viscose, as well as synthetic fibres like polyester and acrylic - from 20 to 200 kg ; 1 Dutch machine for dyeing particularly delicate garments; and finally 5 sampling machines whose capacity varies from 2 kg to 15 kg.
One of the best dyehouses in Europe. © Tintoria Barbara
“The use of these machines allows us to test the best type of garment dyeing to pass after production. The quality and precision with which the samples are made allow an effective reduction of the margins of error in the subsequent dyeing of the order,” the company says.
Fixing
The importance of Tintoria Barbara’s fixing department is growing. Initially its purpose was to provide an additional service to its dyeing service, but today: “We can consider it a decisive step in the success of a product,” the company explains.
The importance of Tintoria Barbara’s fixing department is growing. © Tintoria Barbara
Equipment includes a Fixing Prince, which boasts a capacity of 50,000 pairs of tights per day; Cortese steam foot fixing , with an 8,000 pairs per day capacity; and Fixing Cortese Lancia, which processes up to 8,000 pairs a day; in addition the department also has seamless fixing machines, which can process up to 15,000 pieces per day.
Drying
The production cycle ends in the drying department. Once the dyeing of the garment is completed, it is transported to the appropriate drying section, where staff take care of drying and packing.
Tumble drying at Tintoria Barbara. © Tintoria Barbara
As different fabrics require a variety of drying machines, Tintoria Barbara has three radio frequency belt dryers, which are used for drying pantyhose, an oven for drying at low temperatures, which is used for lighter fabrics and items made from special fibres such as Lurex, and five tumble dryers, which are used for air drying of pantyhose and seamless items in a range of fibres.
Leaving the drying area behind, we come across Renato Moreni, one of three owners and founder of the 50-year-old company. Renato is still very much hands on. He is working with passion together with a small group of employees, physically checking the dye quality of a batch of pantyhose - and this is a company which employs around 80 people and turns over EUR 8 million.
Renato Moreni, hands-on entrepreneur, co-owner and founder of Tintoria Barbara. © Knitting Industry
Apart from servicing the complete Italian hosiery and underwear sector, Tintoria Barbara also works with companies in Spain, Holland and Belgium and is considered to be one of the best dyehouses in Europe.
“To best perform our business, we rely on highly qualified personnel supported by the use of technologically advanced tools. The passion and organization with which we carry out our business are recognized, and the quality of our service makes us proud of our work,” Renato Moreni tells me. “Our current investment programme is for the future.”
Further reading
Castel Goffredo: World class hosiery manufacturing centre
Castel Goffredo: World class hosiery manufacturing centre - Part II
Castel Goffredo: World class hosiery manufacturing centre - Part lll
Business intelligence for the fibre, textiles and apparel industries: technologies, innovations, markets, investments, trade policy, sourcing, strategy...
Find out more